Different types of electric motors used in EVs
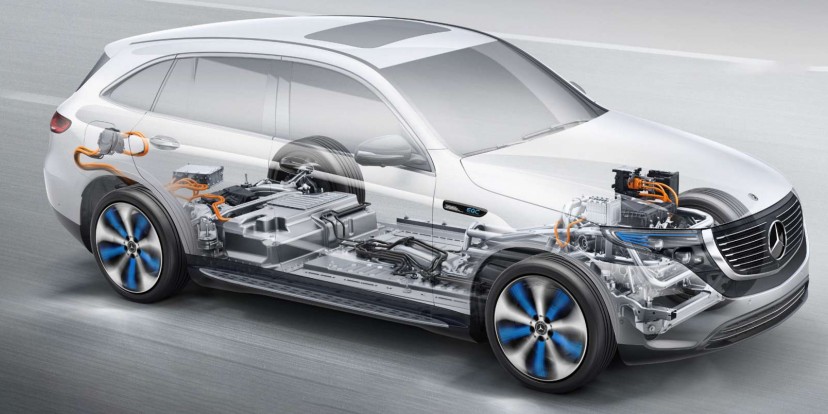
If you are interested in performing a deep dive in internal combustion engine technology, you must be prepared to be bombarded with many different concepts. Naturally aspirated engines, turbocharged engines, direct injection, indirect injection, or both direct and indirect injection! Petrol, diesel, CNG, LPG, Atkinson cycle, Miller cycle, Budack cycle, Diesel and Otto cycle (See Mazda Skyactiv-X engine), fixed geometry turbo, variable geometry turbo, twin-scroll turbo, variable camshaft timing… the list goes on.
The question that almost automatically arises is, why do we have so many internal combustion engine designs and concepts? The answer is simple - because none of them is good enough from an efficiency standpoint. In the quest for improving efficiency, many designs have been introduced throughout automotive history by engineers. Is this variety of designs relevant for the electric motors as well? How many types of motors do we have in e-mobility? The answer is just 3 main ones. Let’s get acquainted with them.
Asynchronous induction motor - Brief history lesson
The asynchronous induction motor isn’t something new. It has been invented by two independent researchers - the one and only Nikola Tesla and Galileo Ferraris. Even though apparently the Italian inventor first developed this motor in 1885, Nikola Tesla was first to file the patent in 1888.
The invention of the induction motor is without a doubt, one of the greatest achievements in harnessing electricity to power our lives. The adoption of this motor type is so widespread these days, that it is very difficult to imagine everyday life without it. Many electric devices use those motors and the vast majority of industrial motors are of asynchronous induction type.
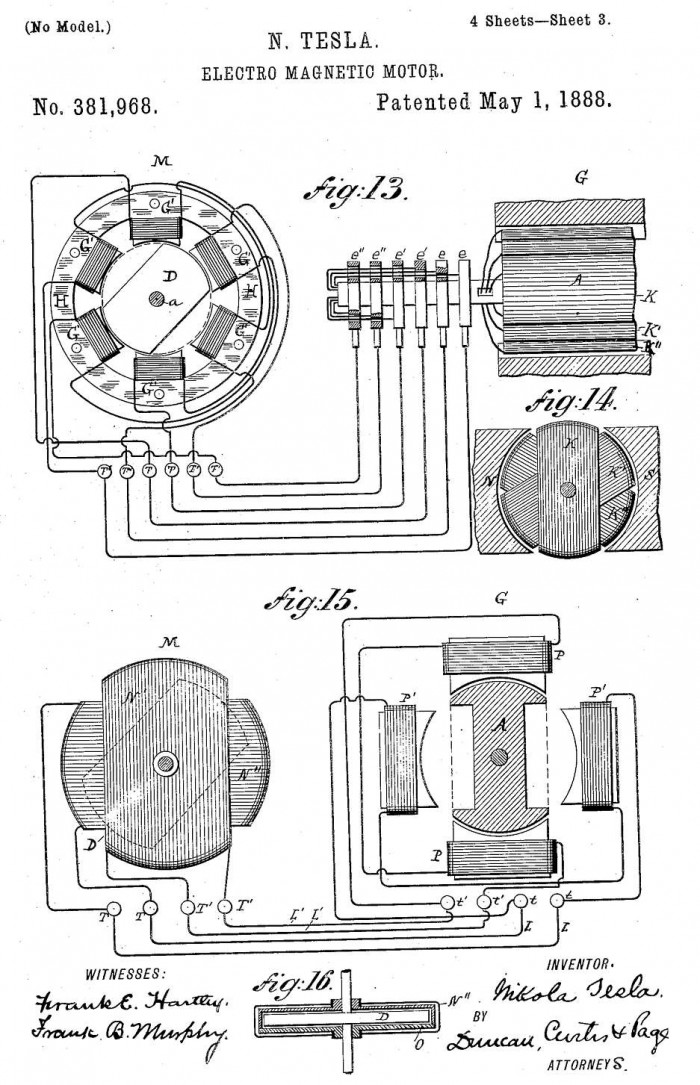
How does an asynchronous induction motor work?
All electric motors have two major parts. A static part is called a stator and a rotating part is called the rotor. Let’s begin with the stator - usually a steel cylinder with slots and copper coils that are weaved with a specific geometry. These coils are fed with 3 phase AC current that has been converted from DC (provided by the battery) in the power electronics. This current creates a rotating magnetic field in the stator and the speed of that rotating magnetic field is called synchronous speed.
In essence, here’s how this type of motor works: AC voltage is put to the copper coils (or windings) and as a result we get a rotating magnetic field, that field induces voltage in the rotor which in turn causes current to flow. That flow of current produces its own rotating magnetic field in the rotor which lags behind the magnetic field of the stator. The force between the two magnetic fields that end up moving the rotor is called the Lorentz Force. The movement of the rotor is then transferred to the wheels of the car through the proper reduction.
This motor is called asynchronous because the rotating magnetic field of the rotor and stator are not synchronized. The induction part comes from the rotating magnetic field, voltage, and current being induced by the stator. When we press the accelerator pedal the rotor’s magnetic field lags a bit behind the stator’s. When we decelerate and the motor works as a generator (regenerative braking), then the rotating magnetic field of the rotor is ahead of the stator. This difference in the rotating magnetic fields is called “slip” and is generally up to 5% depending on the motor design.
Typical efficiency of a 3-phase asynchronous induction motor used in the automotive industry is around 90%. Because of its robustness, simplicity, longevity, and zero exotic materials requirements, this motor is used almost exclusively in industrial processes. Also, its good overload characteristics make it a perfect on-demand motor and that’s why it is often used as a front motor in AWD electric cars.
Pros
- Good efficiency
- Cheap to make
- No need for rare earth materials
- Almost perfect reliability
Cons
- Bigger cooling needs
- Lower power density
- Lower efficiency compared to other motors
Some of the cars using the asynchronous induction motors are: Audi e-Tron SUV, Mercedes-Benz EQC, Tesla Model S, 3, X and Y on front axles and VW Group MEB cars use them on front axles as well.
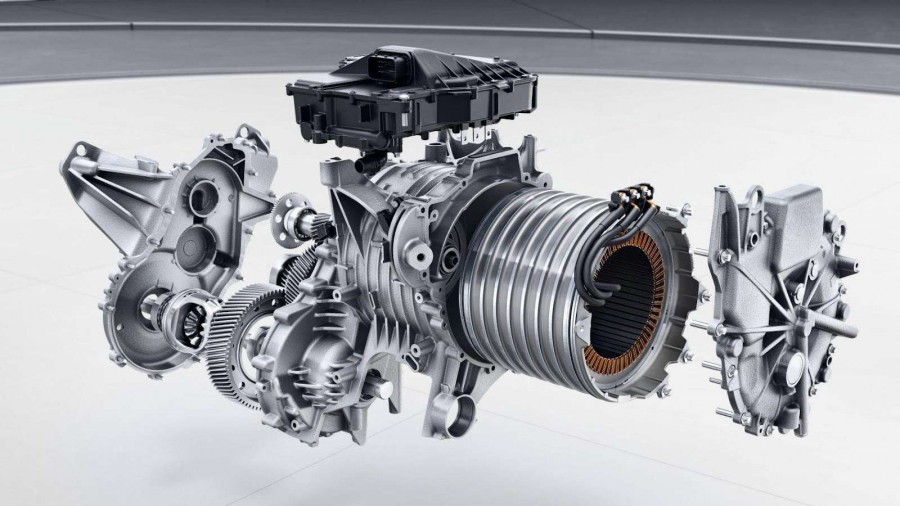
Synchronous permanent magnet motor
The fundamental difference between asynchronous induction motors and synchronous permanent magnet motors is the way in which the rotating magnetic fields in the rotor and the stator are produced and interact. In synchronous permanent magnet motors, there is a native rotating magnetic field, created by permanent magnets (hence the name of the motor) in the rotor. The rotating magnetic fields of the rotor and stator in these motors are locked and there is no slip.
The permanent magnets in the rotor are one of the key elements that increase the power density and improve the efficiency of the motor. The increased power density means high power in low volume, which is why permanent magnet motors are used exclusively in PHEVs. The electric motor in these vehicles is housed in the gearbox and there are space limitations.
Permanent magnets are made from rare earth materials with China controlling the majority of them. There are questions about the ethical aspects of the mining process and for that reason, many manufacturers try to reduce the usage of these materials in their motors. Nevertheless, the synchronous permanent magnet motor is the king of efficiency - it can reach up to 94-95% and when there is only one motor in the car, then this is the type of the motor used.
Pros
- Very high efficiency
- Lower cooling needs
- High power density
Cons
- Production cost
- Need for rare earth materials
- Theoretical danger of demagnetization
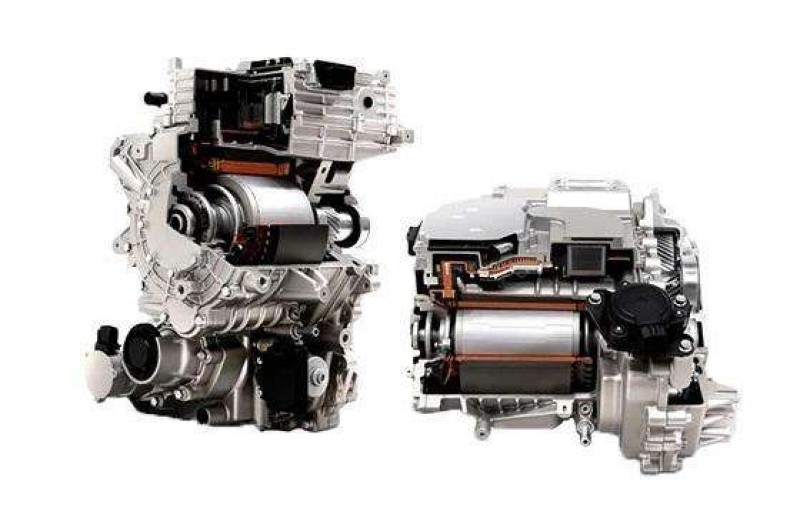
Permanent magnet motors are used in Hyundai Ioniq 5, Kia EV6, Tesla Model S, 3, X and Y on the rear axles. VW Group MEB cars use them as well on the rear axles, Jaguar i-pace, Audi e-tron GT, and Porsche Taycan just to name a few.
Electrically excited synchronous motor
Permanent magnet synchronous motors bring the best efficiency of all, but the rare earth materials required for their construction present implications. To tackle these issues, some manufacturers, namely BMW, Renault Groupe, and Smart currently, use a hybrid motor design - they use synchronous motors that do not require rare earth materials.
So, how do these motors work? Well, instead of using permanent magnets in the rotor to create current, these motors use brushes and slip rings. According to BMW, this kind of motor provides an efficiency of up to 93% which is very close to the efficiency that permanent magnet motors provide. Even though this type of motor appears very promising, the fact that it uses brushes means that it will require at some point replacement of these components. Let’s hope that the manufacturers that develop this kind of motor use brushes with a sufficiently long service life.
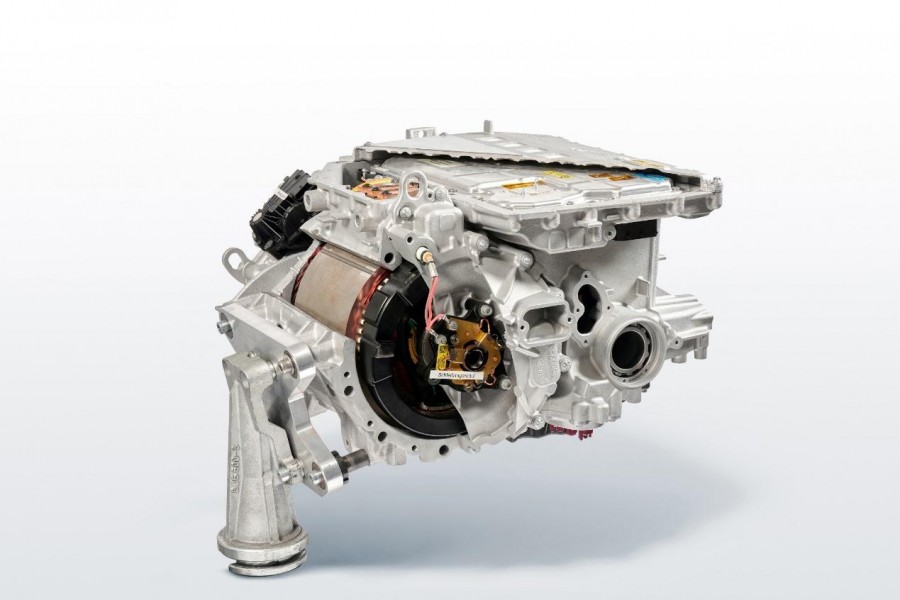
Pros
- Very high efficiency
- Cheaper to make than permanent magnet synchronous motor
- No risk of demagnetization
- No need for rare earth materials
Cons
- Brushes long-term reliability
This type of motor is used by BMW iX3, iX, and i4; Renault Megane E-TECH and SMART EQ.
Related
Reader comments
- Anonymous
best car
- 27 May 2025
- NvX
- kophy landlord
Nice and cute car
- 15 Jan 2024
- CGH