Tesla's breakthrough promises to reinvent car production
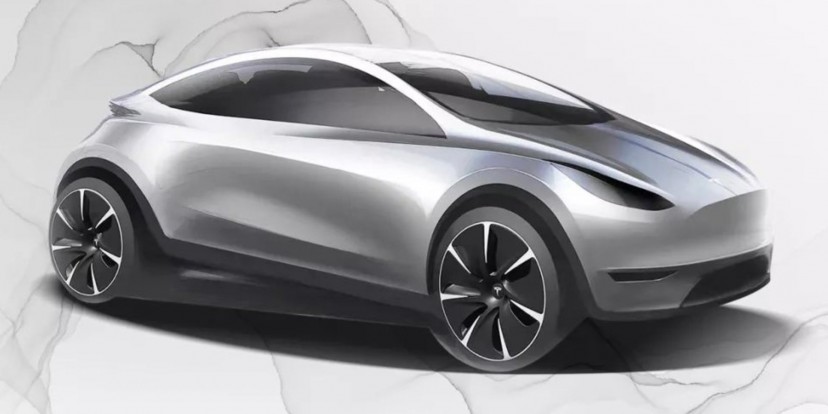
The electric car world, frequently buzzing with innovations, has once again made a major step forward. This time, not by the launch of a new model, but by a breakthrough in manufacturing techniques.
Tesla's recent feats in "gigacasting" have already left competitors bewildered, pushing them to chase the American EV giant. With their mega presses that apply a clamping pressure between 6,000 to 9,000 tons, Tesla has effectively reshaped the production of the front and rear structures of the Model Y. This process drastically cut costs, making traditional manufacturing methods appear, dare we say, quaint.
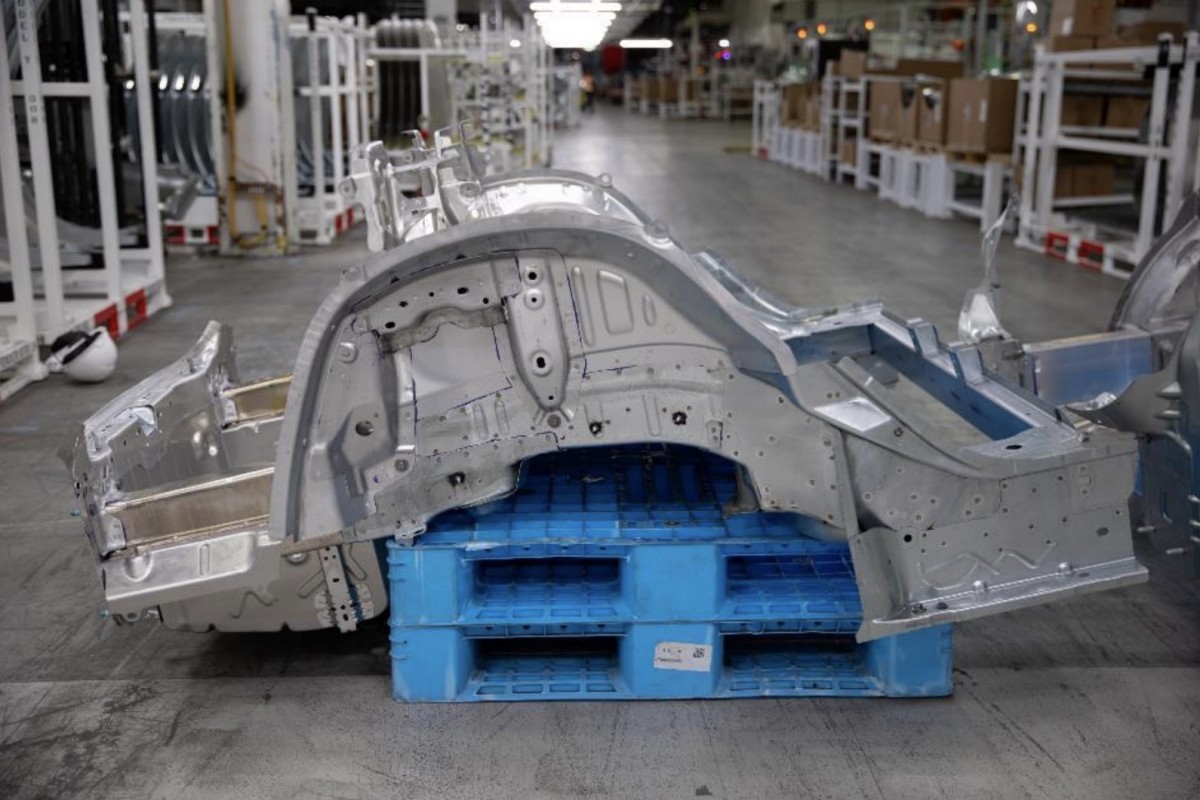
The "unboxed" manufacturing strategy, revealed by Musk earlier this year, is poised to take this a step further. The goal? To die-cast almost the entire complex underbody of an EV as a singular piece. In contrast, a conventional car uses about 400 parts. Picture that: 400 parts reduced to just one. If the word "efficiency" had a picture in the dictionary, this would be it.
Now, you might be wondering, "What's the big deal?" Let Terry Woychowski, president of the U.S. engineering firm Caresoft Global, clarify: Gigacasting most of an EV's underbody would revolutionize car design and production. “It’s a game changer,” says Woychowski, a seasoned vet with over three decades at GM. However, he acknowledges, "Castings, particularly of this scale and complexity, are incredibly challenging."
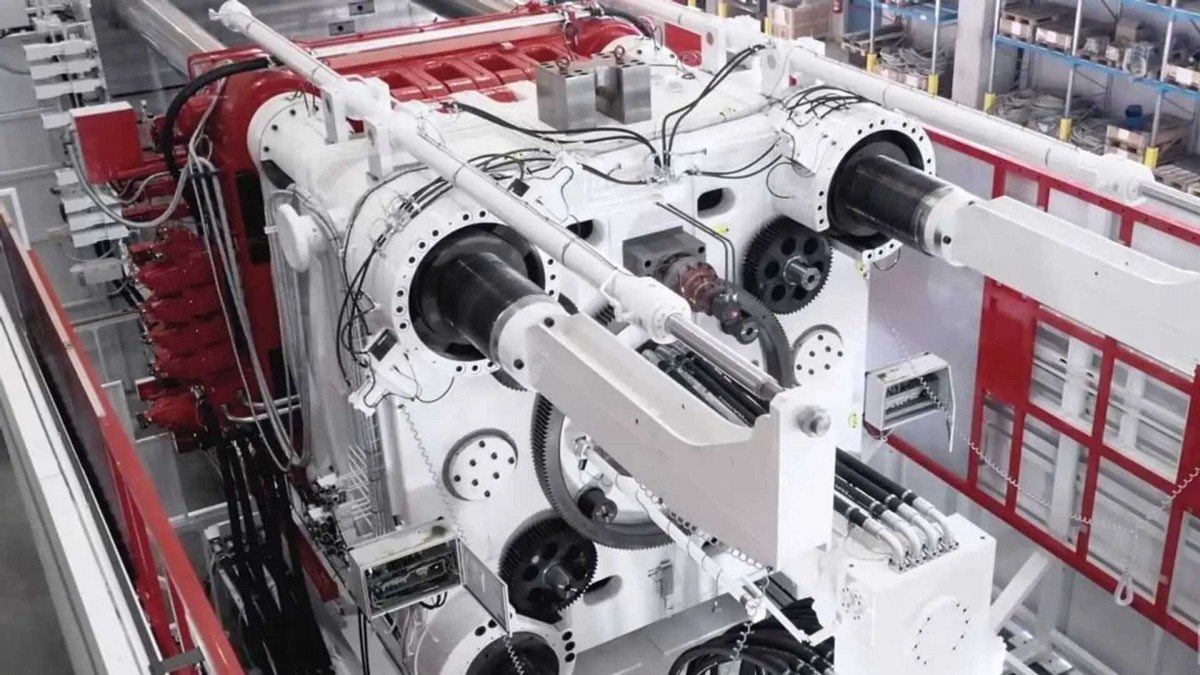
The word on the street is that Tesla's unique design and manufacturing approach could bring a car's development time down to a mere 18 to 24 months. To put it in perspective, traditional manufacturers typically need three to four years. That's like comparing a horse-drawn carriage's pace to that of a space rocket.
And what does all this innovation mean for the consumer? A potential electric vehicle with a price tag of $25,000 by mid-decade. This EV might sport a single large frame merging the front, rear, and central underbody where our beloved battery resides.
But here’s where things get even more exciting (if that’s possible): the true innovation lies in the mold-making process. Traditionally, carmakers have shied away from gigantic structures due to the "gigacast dilemma": high costs, multiple risks, and the potential for exorbitant expenses if tweaks are required.
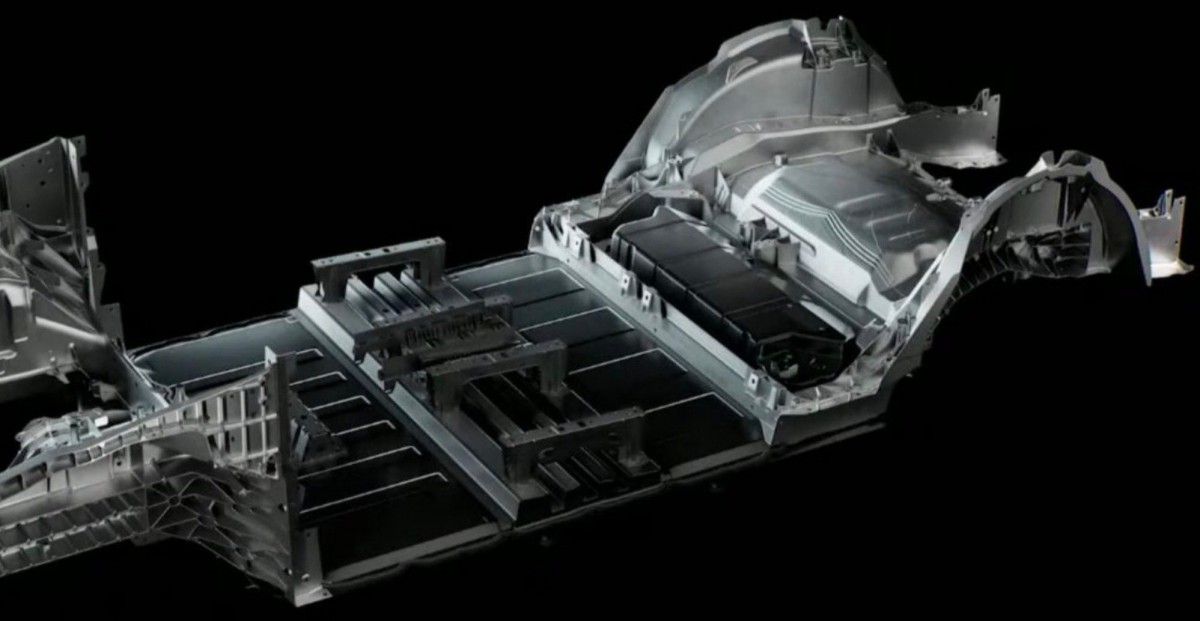
Tesla's solution? 3D printing using industrial sand. With this method, even with several iterations, the validation process's cost is a mere fraction of that with metal prototypes. But every story has its hiccups. Despite the advancements in mold design, Tesla had to navigate the challenges of the aluminum alloys used in casting. Different behaviors in sand and metal molds often fell short of Tesla’s quality criteria. The fix? Tailored alloys, refined cooling processes, and post-production heat treatments.
Interestingly, Tesla’s upcoming small car could be the testbed for this one-piece EV platform approach. Given its simpler design - think less of a hood or rear trunk and more of a "battery tray with wings" - it's an ideal candidate.
However, the journey isn't all smooth sailing. Tesla is yet to finalize the type of press to employ for this endeavor. A high clamping power press can churn out large body parts rapidly but might not accommodate the 3D-printed sand cores crucial for hollow subframes. There's a trade-off between speed and quality - which path will Tesla choose?
Related
Reader comments
- geekso
I don't think this is good news. It happens like with phones and tablets - if something breaks, you throw it away, because the repair costs more than the cost of the device.
- 17 Sep 2023
- M6c
- Debra
It will be repaired "easily" like an iPhone
- 16 Sep 2023
- as0
- MuskFanBoy
Tesla master Race
- 16 Sep 2023
- Ya1